
Raw Mill, Cement Raw Mill, Raw Mill In Cement Plant Cement
Raw mill is generally called cement raw mill, raw mill in cement plant, it refers to a common type of cement equipment in the cement plant. In the cement manufacturing process, raw mill in cement plant grind cement raw materials into the raw mix, and the raw mix is sent
learn more
Raw Mill – Raw Mill In Cement Plant AGICO Cement Raw Mill
Cement ball mill and cement vertical mill are two raw mills commonly used in cement plants. As the main cement equipment in the cement production line, the two cement raw mills
learn more
The digitization work of cement plant in China - ScienceDirect
2023年11月1日 Smart cement plant. AI. Approve operation. Quality control. Intelligent optimization control. Digital production. Intelligent operation and maintenance of
learn more
Reducing energy consumption of a raw mill in cement industry
2012年6月1日 The raw mill considered in this study is located in a cement plant located in Sanliurfa, Turkey. The plant is a single chamber mill with mechanical circulation system
learn more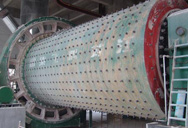
Analysis of material flow and consumption in cement
2016年1月20日 The material efficiency values for a raw mill, pyro-processing tower, rotary kiln, clink cooler, and cement mill are determined to be 36.69%, 34.24%, 39.24%,
learn more
How does a raw mill work in a cement plant? - LinkedIn
2022年12月19日 A raw mill is a key piece of equipment used in a cement plant to grind raw materials into a fine powder. It works by crushing and grinding materials such as
learn more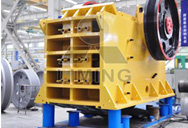
Modeling of energy consumption factors for an industrial cement ...
2022年5月9日 24 Citations. 5 Altmetric. Metrics. Abstract. Cement production is one of the most energy-intensive manufacturing industries, and the milling circuit of cement plants
learn more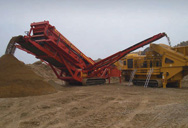
Digitization and the future of the cement plant
2020年9月16日 When envisioning the cement plant of the future, it is important to understand the reference for a typical plant today. Our reference plant is a five-stage preheater-calciner kiln with a vertical raw
learn more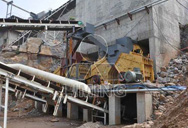
Vertical Raw Mill Cement Raw Mill Raw Mill In Cement Plant
get price! Vertical raw mill is one kind of raw mill, generally used to grind bulk, granular, and powder raw materials into required cement raw meal in the cement manufacturing plant.
learn more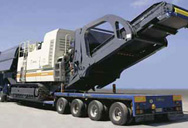
From raw materials Extracting raw materials Raw
2022年2月12日 The most important raw materials for making cement are limestone, clay and marl. These are extracted from quarries by blasting or by ripping using heavy
learn more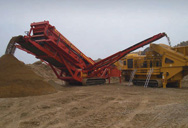
Digitization and the future of the cement plant
2020年9月16日 When envisioning the cement plant of the future, it is important to understand the reference for a typical plant today. Our reference plant is a five-stage preheater-calciner kiln with a vertical raw
learn more
8VLQJ$VSHQ 3OXV6LPXODWRU - IOPscience
simulator was used for the thermodynamic performance of a raw mill (RM) and raw materials preparation unit in a cement plant in Nigeria using actual operating d ata. The raw mill has a capacity of 240,000 kilogram- material per hour. Also,
learn more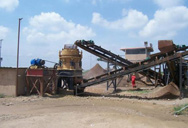
Cement Plant Kawasaki Heavy Industries
Kawasaki Heavy Industries, Ltd. has supplied a lot of cement manufacturing equipment worldwide since its first delivery of a rotary kiln in 1932. The cement plant we designed and constructed has attracted the attention of the world's cement manufacturers and specialists due to its advanced performance. Kawasaki large-scale and energy-saving ...
learn more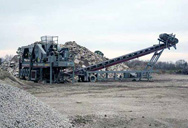
Modeling of energy consumption factors for an
2023年12月4日 the vertical roller raw mill circuits (line 2) in the Ilam cement plant. e critical operating parameters gathered during the standard operation are summarized in Table 1. Variables were monitored ...
learn more
Efficient machine learning model to predict fineness, in a vertical raw ...
2023年3月1日 β [1 − α; p 2; n − p − 1 2] = (1–α) th quantile of β [p 2; n − p − 1 2] distribution. For α = 0.05, the number of outliers is 44 among 280 data corresponding to an upper limit control U C L M a h a l a n o b i s = 4.55 as illustrated in Fig. 3.The results of these outliers have been carefully analyzed by a process expert from the cement plant.
learn more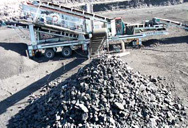
Cement Mill - Cement Grinding Machine - Cement Plant
Coal mill is the main equipment in the pulverized coal preparation process.Because calcining top-grade cement clinker requires a stable supply of coal powder as the fuel of cement kiln, and more than 85% of pulverized coal should be finer than 200 mesh, water content less than 2%, and calorific value more than 6000Kcal/kg, therefore the pulverized coal
learn more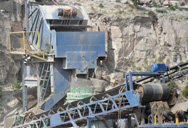
Model Predictive Control for Blending Processes in Cement Plants
2022年1月1日 In the raw mill, raw materials are blended and ground into particles of a desired size. The final output from the raw mill is d n ted as r w m l. Finally, a co veyor belt trans- ports the output raw meal to a homogenizatio silo. T quality standards of the raw meal are det rmined by the oxide c mp sitio of the raw meal.
learn more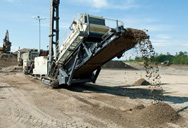
Dust Emission Monitoring in Cement Plant Mills: A Case
2021年8月28日 An important tool to manage raw materials for cement production in any cement plant is the raw mill. Here, the raw materials are brought to the desired dimensions and then placed in the oven. During the size reduction process, dust emissions are managed by air pollution control equipment, bag filters, or electrostatic filters.
learn more
Job Safety Analysis for Various Operations in Cement
2021年2月5日 After crushing, the raw materials are transported to the plant by conveyor. Before homogenized, the plant stores the material. Too finely ground, the materials are transferred to the raw mill, to produce raw mix. The raw mix is preheated before it goes into the kiln, and by the flame, it can be heated to 2000 °c to produce clinker.
learn more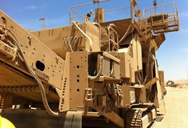
Reducing energy consumption of a raw mill in cement industry
2012年6月1日 About 2% of the electricity produced in the whole world is used during the grinding process of raw materials [1]. While total electrical energy consumption for cement production is about 100 kWh/ton of cement, roughly two thirds are used for particle size reduction [2]. About 65% of the total electrical energy used in a cement plant is utilized ...
learn more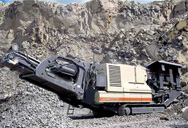
Cement Manufacturing—Technology, Practice, and
2021年11月17日 The grinding operation of the cement is carried out in cement mills located in the grinding plants. The grinding plants can be installed at a far away location from the clinkering plant. 2.6 Cement Dispatch. Cement is shipped in bulkers or in packed bags. Transport can be by road, railway, and waterways and depends on local conditions.
learn more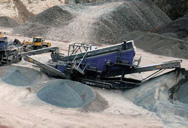
Engr Naveed Ashraf - Senior Deputy Manager
4-Troubleshooting and provision of prompt rectification to the problems occurring in material processing at different areas of the plant i.e. Raw
learn more
Analysis of material flow and consumption in cement
2016年1月20日 In the surveyed cement plant, three balances are established between input and output material in the raw mill, clinker production, and cement grinding system. 2.48 t, 4.69 t, and 3.41 t of materials are required to produce a ton of the product in raw material preparation, clinker production, and cement grinding stages; waste gases
learn more
Raw Material Drying-Grinding - Cement Plant Optimization
Ball mills for cement raw material and coal equipped with a drying compartment adequately air swept with hot gas (2.5-3.5M/sec above the ball charge), can handle moisture about 8%. Fully air- swept mills (5-6M/sec) can dry up to 12-14% moisture. Grinding Operation Objectives and KPIs: Highly energy intensive unit operation of size reduction in ...
learn more
Cement Plant Cement Manufacturing Plant EPC Project
The cement manufacturing plant can be divided into five steps: Crushing prehomogenization: cement crusher crush limestone and other materials and stacker and reclaimer homogenize them. Raw material preparation: use cement mill to process materials into required sizes for cement clinker production. Clinker production: In the cyclone
learn more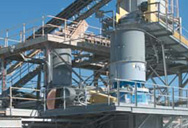
Raw Mix Preparation - ABB
2021年2月16日 • Raw mill control • Closed loop control of feeder set points • Cost minimization ... plays, trends and menus OptimizeIT is an outstanding robust solution for quality issues at the cement plant. It puts the most modern software and control technology at the service of our customers. • Enhanced process stability • Better response to ...
learn more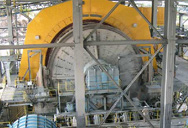
How does a vertical raw mill work? - LinkedIn
Published Dec 26, 2022. + Follow. A vertical raw mill works by grinding raw material such as cement, clay, limestone, phosphate, and sand into a fine powder. This powder is then passed through the ...
learn more
Thermodynamic Analysis of Raw Mill in Cement Industry Using Aspen Plus ...
Positioning of the wires in parallel and in between the plates makes it easy for the electrostatic field of the collecting plate electrodes to remove the dust particles from the gas stream. 4.1 Simulation Data The main purpose of the raw mill plant simulation is to make a simple but realistic model to evaluate the exergy efficiency of the ...
learn more
(PDF) Mining Activities, Cement Production Process and
2022年7月4日 Figure 2.8: Showing the raw mill at stationary, Shayona cement factory. The raw mill has capac ity of 50 tons per hour and takes 300KW of electricity. The mill’s main
learn more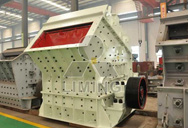
Technological Energy Efficiency Improvements in Cement Industries
2021年3月30日 The cement industry is highly energy-intensive, consuming approximately 7% of global industrial energy consumption each year. Improving production technology is a good strategy to reduce the energy needs of a cement plant. The market offers a wide variety of alternative solutions; besides, the literature already provides reviews of
learn more