
Roller Mill - Springer
2023年7月4日 fl and the device for easy replacement. It can be divided into vertical roller mill, horizontal cylin-der roller mill, high pressure roller mill, Raymond mill, and column
learn more
Optimisation of the performance of a new vertical roller mill
2024年1月15日 The air entrainment can clearly be observed from the bottom region of the mill, indicated by arrows in the upward direction, which can entrain the milled particles
learn more
Review on vertical roller mill in cement industry its
2021年1月1日 In the study the advantages of vertical roller mill are discussed over ball mills. VRM construction, its process and parameters which affects the performance and
learn more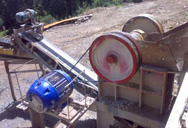
Operational parameters affecting the vertical roller mill
2017年4月1日 Vertical roller mills (VRM) have found applications mostly in cement grinding operations where they were used in raw meal and finish grinding stages and in power
learn more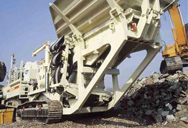
OK™ cement mill The most energy- efficient mill for
2019年4月10日 Proven commercially, the OK™ mill is the premier roller mill for finish grinding of Portland cement, slag and blended cements. The mill consistently uses five to
learn more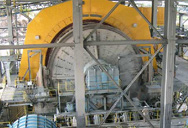
Model and simulator of inlet air flow in grinding
2023年5月22日 models of air ow in the inlet part of the installation and provides a simulation environment for easier testing of various air ow control schemes. Moreover,
learn more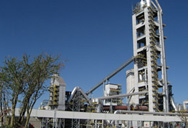
Model and simulator of inlet air flow in grinding installation
2023年5月22日 A comparison of numerous mill designs, such as tumbling (ball, rod, autogenous), roller, stirred, vibratory, centrifugal, jet (fluid energy) mills may be found
learn more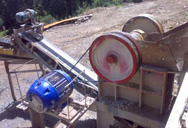
The 3D geometry model of the vertical roller mill.
The 3D geometry model of the vertical roller mill. 1: separator outlet; 2: separator; 3: shell; 4: return hopper; 5: grinding roller; 6: wind ring; 7: air inlet; 8: blade; 9: guide vane....
learn more
PROCESS CONTROL FOR CEMENT GRINDING IN
2017年10月27日 pressure difference between inlet and outlet, the grain size of the raw material [1, 2]. For VRM the production capacity denotes both the capacity of grinding
learn more
AIRSWEPT PENDULUM MILL SYSTEM - Bradley Pulverizer
2021年8月9日 CAPACITY. AVAILABLE IN A RANGE OF SIZES TO MEET YOUR APPLICATION REQUIREMENTS, BRADLEY AIRSWEPT MILL SYSTEMS CAN
learn more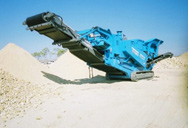
DESIGN AND ANALYSIS OF BALL MILL INLET CHUTE FOR
2019年4月21日 The dimensions/areas for a chute should as far as possible be chosen according to. the outlet flange for a machine. The smallest side length in a chute must be min. 5 times the max lump size. Min. chute size for lumpy material: 250mm x 250mm (0,063 m2). Min. chute size for powdery material: ø200 (0.04 m2).
learn more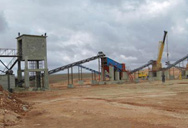
Vertical Roller Mill Operation in Cement Plant
The cement rotary kiln. When operating the vertical roller mill, the operator must control the inlet and outlet air valves to make the air volume of the system in a balanced state, so as not to affect the air pressure at the back end of the rotary kiln. We are AGICO, a professional cement equipment manufacturer and cement plant contractor.
learn more
(PDF) Performance Evaluation of Vertical Roller
2017年9月11日 Due to the compact design and material transportation system of vertical roller mills (VRM), some important streams (total mill feed and discharge, dynamic separator feed and reject) remain in the ...
learn more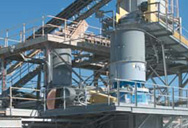
Ball Mill Design/Power Calculation - DESIGN AND ANALYSIS OF BALL MILL ...
2015年6月19日 Ball Roller Power Calculation Model #1. A wet grinding ball mill in closed circuit is to be detective 100 TPH of a substance with a work index of 15 and a size distributor of 80% passing ¼ inch (6350 microns). The required product size market is to breathe 80% passing 100 mesh (149 microns). ... efficient efforts have be made to
learn more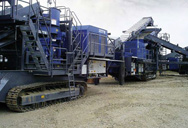
STUCCO PRODUCTION WITH ROLLER MILL - Grenzebach
2021年2月23日 For the roller mill calcining system Grenzebach proposes an indirect stucco cooling system with a rotary tubular stucco cooler to suppress uncontrolled calcination of hot material.To maintain constant cooling conditions in the stucco cooler, the cooling air inlet temperature is controlled to counteract variations caused by ambient temperature
learn more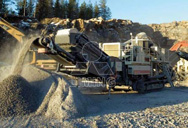
Holderbank Cement engineering book - Archive
2021年1月28日 This paper deals in first place with roller mills for raw material processing. For grinding coal, slag, cement, etc., adaptations to mills and systems have to be made. 2. FUNCTIONS OF THE ROLLER MILL. The vertical roller mill fulfills 4 main functions in one compact piece of equipment: ¢ Grinding.
learn more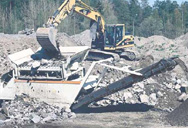
Optimisation of the performance of a new vertical roller mill
2024年1月15日 Sun et al. [9] carried out study of a roller mill (HRM 4800 by Hefei Zhong Ya, China) and analysed air flow patterns in the mill to improve the energy efficiency of the mill. Shah et al. [ 10 ] used modelling to optimise the performance of a coal pulveriser by studying the influence of variation in inlet vane angles on the collection efficiency ...
learn more
Energy-Efficient Technologies in Cement Grinding IntechOpen
2015年10月23日 Vertical roller mills are developed to work as air-swept grinding mills. Roller mills are operated with throughput capacities of more than 300 t/h of cement raw mix (Loesche mill, Polysius® double roller mill, Pfeiffer® MPS mill). ... The rejects from the TSV™ classifier are returned by gravity to the mill inlet. The main features of the ...
learn more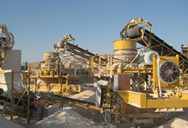
Raw Material Drying-Grinding - Cement Plant Optimization
Primary roller mill controls are: Mill drive power or mill differential pressure to control mill feed rate. Inlet gas temperature. Outlet gas temperature. Outlet gas flow. Few countable salient Features of Vertical Mills. They are air swept mills, therefore has a higher drying capacity to handle an aggregate moisture of up to 20% in raw materials.
learn more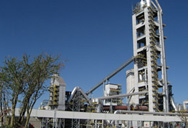
Operational parameters affecting the vertical roller mill
2017年4月1日 In the air-swept mode, the vertical-roller-mill and a high efficiency dynamic classifier are suited above each other as a single unit (Fig. 1). Material is fed to the grinding chamber and transported by table rotation to the grinding gap between the fixed grinding rollers and the mill table. Crushing and grinding take place by compressive grinding.
learn more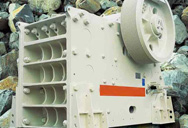
(PDF) Increase productivity of vertical roller mill
2021年1月29日 x Blockage of pressure tapping, particularly mill inlet and air flow measurement points. OK. OK. x Out of calibration bed depth monitors other instruments like PT, TT etc. Found OK.
learn more
OK vertical roller mill - Environmental-Expert.Com
2019年6月29日 - OK vertical roller mills use 30-50% less energy than ball mill systems - Simple layout and fewer machines in the mill circuit ensure high run-factor and ... Air inlet 1 OK mill 2 Dynamic separator 3 Bag filter 4 Fan 5 Magnetic separator Mill arrangement and nozzle ring bypass system OK mill feed composition 100 90 80 70 60 50 40 30 20 10 0
learn more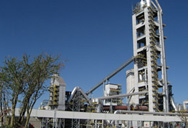
The 3D geometry model of the vertical roller mill.
Download scientific diagram The 3D geometry model of the vertical roller mill. 1: separator outlet; 2: separator; 3: shell; 4: return hopper; 5: grinding roller; 6: wind ring; 7: air inlet; 8 ...
learn more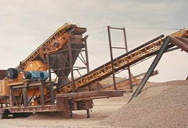
The working principle of vertical roller mill - ITPUB博客
2015年3月9日 The working principle of vertical roller mill. Working principle of vertical roller mill is driven by motor reducer rotating disc, and the hot air from the air inlet into the vertical mill, the material from the feed opening falls on the disc center, due to the centrifugal force, the material is moved from the center to the edge of the grinding ...
learn more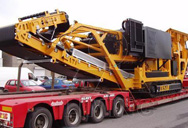
OK™ cement mill The most energy- efficient mill for
2019年4月10日 Proven commercially, the OK™ mill is the premier roller mill for finish grinding of Portland cement, slag and blended cements. The ... Air inlet 1 OK™ mill 2 Dynamic separator 3 Bag filter 4 Fan 5 Magnetic separator Mill arrangement This schematic illustrates a typical grinding installation. The arrange-
learn more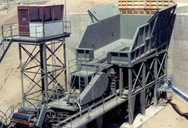
(PDF) Design and Analysis of Ball Mill Inlet Chute for Roller
The designed new truck for mill inlet chute for UMS ball millmodel as given below (Fig 5.2). The hollow square section. was used as supports in all the sides of the truck frame. 5.5.2 Feed Chute with Truck Assembly. 8/12/2019 Design and Analysis of Ball Mill Inlet Chute for Roller Press Circuit in Cement Industry. 7/8
learn more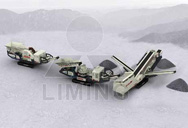
Ball mill for cement grinding - FLSmidth
The feed chute is lined with bolted-on wear plates and slopes down through the air duct to the mill inlet opening. The stationary steel plate inlet duct leads the venting air into the mill. It is equipped with a manually operated throttle valve and a pressure monitor to adjust the pressure at the inlet end, thus preventing dust emission from ...
learn more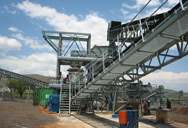
Coal Mill in Cement Plant Vertical Roller Mill Air-Swept Ball Mill
It is a mechanical device used to grind raw coal into pulverized coal powders. The most used coal mills in cement plants are air-swept ball mills and vertical roller mills. At present, most cement plants use coal as the main fuel in the clinker production process. The standard coal consumed by the new dry process for producing 1 ton of cement ...
learn more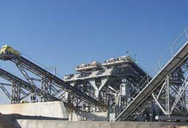
Feed chute for vertical roller mill - Google Patents
the fluidized material When aerated, the fluidized material will flow downwardly above gas permeable member 10 from the inlet to the outlet by gravity. In operation, it is normal to supply ambient air to the lower plenum chamber 11. The air under pressure flows upwardly through gas permeable member 10 to aerate and fluidize the material in the upper
learn more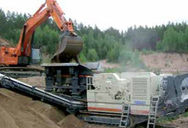
WO2021093255A1 - External circulation roller type vertical mill ...
There is an air inlet cylinder 30 at the lower part of the powder selection cylinder. There are one or more air inlets 15 on the air inlet cylinder 30. The airflow entering the air inlet cylinder 30 rotates upwards and enters the powder selection area through the air guide blade 10 to separate the incoming materials. The coarse particles cannot ...
learn more